Norton Incinerator Specifications by John W. Norton, P.E., B.C.E.E.
Norton
Engineering has developed over the years a complete design for a
large municipal incineration system with energy recovery. Mr. Norton
personally designed and built two such systems, one with energy
recovery and one without, and operated both of these systems for more than four years.
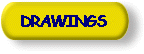
If any civic
body or government entity contracts with Norton Engineering to build
one, or more, of these systems, Mr. Norton and his staff of
experienced engineers will design, draw, and specify all of the
necessary incinerator components for the Municipal Incineration Plant
housing one or more 250 Ton per Day (TPD) Municipal Incinerators, to include:
- equipment
foundations, as necessary
- all trash
storing and receiving areas
- all trash
handling systems
- all trash
combustion systems
- all energy
recovery systems
- all
interconnecting duct work
- all air
pollution control systems
- building
layout plans
- all control systems
- all
electrical distribution systems
- all motors
and transmissions
- all ash
extraction equipment
- all ash
handling systems
- all ash reuse
manufacturing systems
Designs,
calculations, drawings and specifications shall be prepared by Norton
Engineering's experienced staff using computer based office and
engineering systems. This engineering service on this Project shall
be performed exclusively for the contracting agency. Some of this
engineering service may be subcontracted by Norton Engineering where
it seems likely that subcontracting will save project expense.
Drawings will be reproduced on AutoCAD computer based drafting systems.
If the
contracting agency is interested, Norton engineering can assist the
agency to have much of the work and components manufactured in the
vicinity of the contracting agency, Korean Companies for example.
The
Basic Services of this proposed Work includes:
- fabrication drawings
- equipment
designs & layout drawings
- 4 design
meetings, as and if necessary, away from the Engineer's home city
office by Mr. Norton and/or his designated agent(s), and reports of same.
- bid drawings
-
specifications for manufacture and supply
- fabrication
bid evaluations and reviews
- construction drawings
- assembly and
erection drawings
- 5 site
inspections of 12 day duration by Mr. Norton or his designated
agent(s) and reports of same.
The proposed
plant shall be designed to be similar to the ones designed, built,
and operated by Mr. Norton for Montgomery County in Dayton, Ohio.
This engineering service will be performed so that officials and the
public may inspect its superior ability to destroy wastes while
producing energy and useful construction materials.
The Project to
be built for demonstration purposes will be capable of burning in
clean combustion 250 long tons of mixed municipal solid waste with
limited water content per incinerator line. This demonstration plant
will produce ash of only approximately 10% volume of the incoming
waste. This ash will be processed to recover steel and produce usable
construction materials such as roadway base (substitute for sand and
crushed rock) and construction blocks. Ash product can be used for
road construction base if washed and cured with cement.
Heat released
from this combustion shall be used to make steam to generate
electricity. Some steam may be used for industry at their connection expense.
Construction of
buildings and installation of equipment can be by contracting agency,
Korean Companies for example. Also some equipment manufacturing can
be done in Korean factories and machine shops.
When the first
plant is demonstrated to be successful, others can be built from the
same and improved plans. Perhaps more machinery can be manufactured
in Korea (or another contracting vicinity) for subsequent plants
after the first one is demonstrated to be excellent.
ESTIMATED
FACILITY SIZE & SPECIFICATIONS
Contracting
entities shall supply a site appropriate for construction of the
proposed facility. The very best land size for a solid waste
incineration facility is approximately 40,000 square meters on a hill
side, although a plant can be designed for a smaller site. The
incinerator plant footprint is to be approximately 10,000 square
meters. Ash processing and energy production will require more space.
A hill side is good because the building can be adapted to a slope
which accommodates 5 standard floors of elevation in approximately
100 horizontal meters. The incinerator has an entrance about 15 M
above the ash truck loading floor. Thus, the facility may be made to
conform to a slope.
The exhaust gas
stack (chimney) should extend above the general terrain in the
immediate vicinity of the plant, in order that the combustion gas
products be adequately dispersed. Adjacent hills shall not be so tall
as to hinder stack gas dispersion from a 35 meter tall stack.
The appearance
of the plant (to be constructed by others) should be in keeping with
the architecture of similarly sized manufacturing facilities. Trash
truck deliveries will be kept indoors to minimize odor and disorderly
appearances. Ash handling and processing will be kept under roof and
indoors so that it is not offensive to the neighbors and also so that
operations may be conducted year round in all types of weather.
There will be a
cooling tower ( perhaps 3 meters high and 15 meters square) that will
emit a white cloud of clean water vapor during many seasons of the
year -- especially during the winter.
Bunker areas
for the storage of completely processed ash, ready for use as sand
substitute will be designed into the Project.
ESTIMATED
ENERGY PRODUCTION
After
completion, the facility will produce an approximate average of 3 to
4 megawatts of electricity per 250 TPD incinerator line, more if
solid waste is high in energy content. The machinery will only
require approximately 0.7 megawatts per 250 TPD line for operation.
Thus, this facility is likely to produce a net benefit of 2.5
megawatts of electricity while it destroys 250 TPD of mixed municipal
solid waste and produces steel and sand substitute for sale.
The proposed
plant will be patterned after the two municipal incinerator plants in
Dayton, Ohio, which historically received approximately 500,000 tons
of waste each year and managed to burn nearly 80% of that material.
The energy recovery system on the prototype line in Dayton operated
successfully for seven years, producing about 5 megawatts of
electricity during its 90% on line time until all incineration ceased
in Ohio. Ash from the incinerators was used successfully for road
base for many miles of asphalt bicycle paths along Dayton's rivers
and it has also been used in concrete blocks which have been used to
construct two large buildings.
PROCESSING
PLAN
The
incineration chamber will be designed to include an auxiliary gas or
oil burner to be used as necessary to maintain the proscribed minimum
combustion temperatures. Experience, however, indicates that use of
the burner will not be necessary to maintain temperatures of 700oC,
or higher. In practice some dry solid waste which makes good fuel
should be held back for times of trouble. This is typically cardboard
or wooden scraps.
The residence
time for gaseous products in the hot combustion chamber will be
designed to be at least 1 second to insure a good burnout.
Temperature recording devices will keep a continuous record of the
temperatures in areas of interest such as the primary combustor, the
air pollution control equipment, and the exhaust stack.
Overfire air
will be introduced in a fashion to provide good mixing of the
combustion products. Video cameras will be installed for viewing from
the main control room so that human interpretation of the combustion
conditions can be made continuously. There is no substitute for a
good human eye when trying to make an efficient fire.
Temperatures of
critical points, flows of gases and water will be monitored by an on
line computer capable of warning the operator of unusual conditions
and in some cases of making the necessary changes. One good example
of such computer controlled ability is the control of the vacuum
strength by computer adjustment of the fan dampers.
The combustion
chamber will be constructed of stout steel members and a steel shell
(minimum thickness 4 mm). The steel shell will be protected from the
fire with a combination of refractory brick and poured and plastic
refractory of good quality meeting or surpassing Korean Industrial
Standards. Access doors for maintenance will have little windows for
careful viewing of the fire. The outside surfaces of the combustion
chambers will be kept to no more that 80oC
by the use of adequate refractory and insulation materials.
The steel shell
will be fully welded to provide an air tight enclosure for the
combustion. This will prevent the careless inflow of air to the fire
and the escape of any combustion products in an uncontrolled fashion.
The appearance of the outside of the incinerator will be maintained
in first class condition by the use of fireproof paint, or other
protective materials of good appearance.
It is also
possible to automate stack monitoring for opacity, temperature, and
flow and CO2
content. For additional cost, it would be possible to install
automatic systems for such recording.
DESCRIPTION
OF THE COMPONENTS
In the course
of the specific design of this project, changes in the design of
these following components may be made in order to accommodate
regional requirements and practices, and manufacturing capabilities:
SCALES:
The new Norton Engineering Incinerator will have entrance scales for
all incoming waste to provide an electronic readout so that a daily
record will be generated showing such information as source of trash,
amount, driver's name, etc. This will allow computer analysis of the
entire waste receiving (and accounting) function.
TIPPING
FLOOR AND ENCLOSURE:
The tipping floor will be completely enclosed and combustion air for
the incinerator withdrawn from this area to insure that clean air is
constantly drawn into this front end area. This insures that odors
and dust are captured and incinerated, thus destroying both.
The tipping
floor area will include machinery for gross separation of incoming
solid waste so that moisture can be minimized. Many vegetable/organic
items will be conveyed away from the combustible solid waste storage
area so that they can be composted, and not burned.
FIRE
PROTECTION:
The Norton Engineering Incinerator will have a manually controlled
solid waste storage spraying system similar to an automatic fire
sprinkling system. This can be activated quickly in the case of solid
waste storage fire, and as needed to control dust during dry seasons.
Television
monitors will be installed in the storage area so that the combustion
control board operator can keep track of the movements of the crane
operator and help to keep "fire watch."
INCINERATOR
ENTRANCE AREA FEED HOPPER:
The entrance feed hopper will consist of a heavily reinforced
concrete funnel. The concrete used will be high strength, 35 MPa.
HOPPER
LIDS:
The entrance hopper closing lids will have a pivoted lid normally
held in a position which allows gravity to close it. This system will
have a manual clutch which an operator can disengage--if power fails
for any reason and the lid must be closed. It is critically important
on occasion to get the hoppers closed off quickly. If power has
failed, for example and the trash burns down in the feed chute, then
(in the absence of forced draft) the fire can come back up the chute
and damage the roof or ignite the stored solid waste.
FEED
CHUTE:
The feed chute will be refractory lined. While this refractory does
wear, it is very slow and predictable. It will be constructed of
simple straight refractory bricks. The feed chute "arch" at
the bottom of the feed chute will be a poured refractory arch.
IGNITION
AREA CEILING: The
ignition chamber ceiling will be established at a height that will
allow for a large area for heat energy release. The arch in this area
will reflect heat back onto the trash and deflect hot gases back onto
the drying grate area for drying the trash in times of high moisture.
DRYING
GRATES: The
drying grates will be constructed of 309 stainless steel. These may
be cast alloy or may be welded at local machine shops depending on
pricing and availability. Their uniform design will allow a reduction
in inventory of spare parts.
AIR
COOLED BEAMS:
Between section of grates, air cooled beams face the fire. They are
fabricated of 309 Stainless Steel.
IGNITION
GRATES:
The Ignition Grates are to be fabricated of 309 Stainless Steel.
These grates are attached to fabricated steel support beams (or
"Stringers"). These stringers are to alternate--one movable
between two fixed. There are to be thirteen across the ignition and
drying areas--six movable and seven fixed.
These grates
should be easy to install and replace, and can be repaired in the
unit with welded patches, as can the drying grates above. Several
local fabricating shops should be able to bid on the work with
resulting competition and economy.
These grates
will have underfire air slots although much of the underfire air will
pass between the separate grate stringers. It is believed that this
is a good point of passage for the majority of the air because this
is the one area constantly kept open by the reciprocating action of
the grates.
FLAPPER
SEALS:
The upper end of each grate section will be protected from solid
waste by flapper seals made of 309 Stainless Steel attached to the
fixed (stationary) grates.
GRATE
DRIVES:
The grates are to be driven by push rods fabricated from a single
piece of rectangular steel for added strength and ease of
fabrication--bushing sleeves will be added to each pin connection.
Hydraulic drives could be used on the grates if this is desirable to
the owner. It is thought that this might provide a substantial relief
from pin and linkage maintenance, but it would carry with it an
unknown amount of hydraulic system maintenance.
REFRACTORY
ROOF:
The refractory roof will be constructed of "Super Duty"
hanging brick--equal to either Detrick, or Chicago Fire Brick. This
system is supported by 8 CM "I" beams on 40 CM centers.
REFRACTORY
SIDEWALLS--UPPER: The
upper sidewalls of this unit are to be 0.5 M thick. These thick
walls provide a huge reservoir of heat energy to buffer the
temperature resulting from varying fuel characteristics. These heavy
walls help resist and buffer explosions which can occur in the
furnace from various mixed waste.
REFRACTORY
SIDEWALLS--LOWER:
The lower sidewalls of the Norton Engineering Incinerator are to be
Silicon Carbide refractory. This system uses tongue and groove
silicon carbide brick shapes with metal tie backs to provide a rugged
cooled surface near the grates where the burning trash rubs the
sidewalls. Air is forced behind the silicon carbide bricks for
cooling, and this heated air is used for underfire and overfire air.
(After it has been used to cool the sidewall in this area it is about
110 oC.)
This lower
sidewall cross section will consist of 10 or 12 CM of silicon carbide
refractory, a 12 to 15 CM airspace (for cooling), and a conventional
straight brick backup wall which in total gives a wall 50 to 65 CM thick.
UNDERGRATE
HOPPERS:
The drying grate hopper is to consist of a smooth, steep funnel and
chute to pass the grate siftings down to the ignition grate hoppers
with minimum dust or emissions.
IGNITION
GRATE HOPPERS:
The ignition grate hopper will also consist of a smooth, steep funnel
that passes the grate siftings down into a flooded drag conveyor
which is intended to pass siftings from the ignition grates and kiln
seal up and into the ash drag conveyor without dust or smoking. This
will allow the maintenance of a positive air pressure under the
ignition grates while keeping grate siftings in air tight conveyors
while it is passing out through the system. (Close personal
inspection of many competitor plants indicates that the positive
underfire air situation is actually seldom attained in
practice--except for short periods of time under ideal test conditions.)
ROTARY
KILN: The
rotary kiln will be designed with variable speed control to function
as the final burn out grate. Slow turning speed of about 4
revolutions per hour will allow the waste to dry and break down
before it is dropped into the ash removal conveyor.
The rotary Kiln
design has excellent characteristics for solid waste that is heavy
and containing more moisture. A reasonably tight air seal is to be
provided to control the amount of air allowed to enter the combustion
process at either end of the kiln.
KILN
REFRACTORY:
The Norton Engineering Incinerator uses a 30 CM super duty wedge type
brick system with no special insulator bricks. This brick lining
should give an average skin temperature of 200 oC,
and a useful life of about 18 months for the quickest wearing area,
the 4 M near the discharge end. The 4 M on the inlet end should last
up to 3.5 years. Operating conditions such as temperature can
increase or decrease the life expectancy of the kiln refractory.
KILN
OVERPASS:
The kiln overpass shall consist of a steel duct lined with super duty
refractory. Its ceiling is to be made of super duty brick shapes
supported by 6 CM "I" beams on 40 CM centers. The object of
the kiln overpass is to provide a passage for the easily volatilized
gases from the primary combustion zone, allowing them to quickly burn
out without causing rapid gas velocity in the rotary kiln.
RESIDUE
(ASH) CONVEYORS:
This is the most troublesome area in plant operations. The Norton
Engineering ash removal system is to be designed with high strength
to resist the wear and binding inclinations of the metal laden ash
material. It will be a heavy drag conveyor submerged in water at the
ash removal area to maintain the positive seal on the combustion area
and quench the burned out, red hot ashes. The conveyor chain will be
approximately 22 CM pitch high alloy cast steel with ultimate
strength of 160,000 KG.
The design will
locate the ash conveyor where it cannot flood, above ground. Design
should provide easy access to the ash conveyors for heavy equipment
for maintenance. There will be easily employed backup systems. The
conveyor flights will be closely spaced to prevent material from
wedging between the flights and the conveyor trough walls. The
conveyor will have a drive assembly at each end to allow for power
reversing. The drive will be hydraulic to eliminate the shear pins
and provide heavy force at slow speed.
The design will
have the shortest drag conveyor possible to dump the ashes into a
large ash storage pit. Wheel loaders will be used to load the ashes
onto highway dump trucks for the trip to the ash processing site, if remote.
CONDITIONING
CHAMBER, OPTIONAL:
Even though a boiler is to be installed and used as the primary gas
cooling device prior to the air pollution equipment, it is
recommended that a conditioning chamber be installed in parallel with
the boiler to provide for continued operation when the boiler is down
for maintenance, or steam is not required.
A conditioning
chamber is a tool with which to gain a substantial operating
advantage. It consists of a refractory lined steel chamber,
temperature controlled water sprays to lower the gas temperature, and
an exit thermal couple to read the exhaust temperature. The new
conditioning chamber would include a submerged drag conveyor and
water air seal through which to remove fly ash. Excess cooling water
that falls on the floor of this chamber would overflow though the air
seal dam and be cleaned up and recycled for use in the temperature
control system to avoid sewer charges.
A control
damper located in the exhaust duct from the conditioning chamber
would allow the flue gases to be directed to the boiler. This damper
could be used to control the amount of heat going to the boiler in
the same fashion that fuel control is used for this purpose in a
fossil fueled boiler.
BOILER:
The boiler shall be designed with smooth tubes and wide gas passages
to minimize the wear during operations. The boiler will use
relatively low pressures and temperatures so that high temperature
corrosion is minimized. The boiler, if by ABB/Alston Power Company,
may be constructed in Korea.
TURBINE
GENERATOR:
The turbine generator will be highly efficient for making electricity
and designed to accept the relatively low temperature and low
pressure steam developed by the boiler. The turbine if by Coppus
Murray, will include an OPTIONAL steam extraction port for later use
in the supply of steam energy to manufacturing facilities if that
becomes more economically reasonable than continued maximum electric
production. Steam from the exhaust side of the turbine will be
condensed for reuse in the boiler.
AIR
POLLUTION CONTROL:
The Norton Engineering Incinerator will employ highly efficient bag
houses or dry electrostatic precipitators for particulate removal.
The preferred method of particulate control is the electrostatic
precipitator (EP) for the following reasons:
-The EP has
less pressure drop across it than a baghouse. This results in much
less energy consumption during operations.
-The EP will
not "blind" as a bag house will from the great percentage
of sub micron particulate that an incinerator generates.
-The EP is less
susceptible to "crusting" from sticky fly ash, and if these
substances do coat the EP collection surfaces they can usually be
"burned" off by temporarily elevating the EP temperature to
approximately 375 oC.
-The EP is less
susceptible to damage from temperature excursions than a bag house.
Incinerator temperatures sometimes vary with surprising speed--for
example during a water failure in the conditioning chamber.
-The EP is less
susceptible to damage from smoldering embers which are occasionally
carried back to the control device.
The
electrostatic precipitator is the collection device of choice when
the whole picture is considered: down time, operating costs, capital
costs, life expectancy, replacement parts costs, and risks associated
with catastrophic failure (such as bag house fires.)
The proposed
plant can meet any specified emission limits. It is wise to demand
the same air emission limits as a modern coal or oil fired power plant.
ASH
PROCESSING:
The ash processing system will include machinery for separating and
stabilizing the ash product with lime and cement so that it can
safely be used in construction for fill material or as construction
blocks. Synthetic aggregate product may be safely stock piled for use
in large projects. Steel and other metals will be recovered for sale
to steel mills and other raw metal processors. Very little, if any,
material will be left over and require landfilling after the ash has
been processed.
|